Bushings Increase MTBR of Heater Drain Pump to Eight Years
Pumps & Systems Magazine, March 2021
By Eric Ford, Graphite Metallizing Corporation
A full-service pump repair company with two strategic complete manufacturing centers located in Barre, Massachusetts, and Monroe, North Carolina, received a contract to rebuild a heater drain pump for a nuclear power plant in the Northeastern United States.
The multistage vertical pump had been in service for eight years, and it was time for a complete overhaul. Eight years before, the original pump bearings were replaced with graphite/ metal alloy bushings in order to increase meantime between repairs (MTBR), reduce maintenance and benefit from the self-lubricating and high-temperature characteristics of the material.
In a power plant, the heater drain pump sends the drain water directly back into the feedwater system, thereby increasing the efficiency of the power generation. Water comes from the condenser to the condensate pump to the heaters, and then those feeder pumps drain the water back into the system. The reliability of the heater drain pump is important for the power plant to run efficiently.
The contract was to overhaul a heater drain pump for a 1,100 megawatt (MW) unit. The internal element removed from the pump well is driven by a 1,250-horsepower (hp) motor with 1,800 revolutions per minute (rpm), 5,430 gallons per minute (gpm) and 770 feet of head. The heater drain water temperature is 370 F. 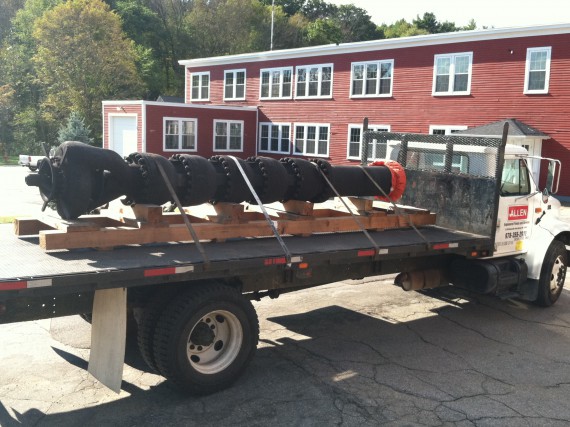
Upon inspecting the existing bushings, the pump repair company found that after eight years of service, the running clearance had opened (increased) by only 0.003 inches to 0.010 inches from the original specifications. Since they were going to do a complete pump overhaul, they decided to also replace the bushings. There had been a slight increase in vibration, but the bushings were still working well.
The repair shop’s customer specified the use of the same nickel-grade graphite/metal alloy for the suction bell bushing and intermediate bearings. These bushings have many features that make it a good fit for this nuclear power plant application. These benefits include:
A self-lubricating material that can withstand dry-run conditions if there is an upset of the pump flow. This is a crucial advantage for equipment that runs all the time. It handles low lubricity fluids such as light hydrocarbons, liquefied gases and hot water in which metal bearings can wear excessively.
Because of the self-lubricating feature, there is no regular bearing maintenance required.
The material can withstand higher temperatures than many polymer bearing options. It runs at
temperatures well above the limits of plastics—even in molten metals above 1,000 F—and has survived extreme thermal shocks, as shown by a series of tests conducted and documented by a major pump manufacturer.
Graphite/metal alloys are dimensionally stable when submerged and will not absorb liquids. They resist attacks by most corrosive liquids, including sulfuric acid, chlorine water and caustics. These alloys maintain dimensional stability when submerged, under static pressure loading and over wide temperature swings, providing constant running clearances for all operating conditions.
The materials are nongalling and will survive extended dry-run episodes. Galling is a phenomenon that is almost like melting together or fusing together. It is a form of wear caused by adhesion between sliding surfaces. As a result of being nongalling, these materials permit closer running clearances between rotating parts resulting in higher pump efficiency and lower shaft vibration.
Graphite/metal alloys survive “loss of pumpage” operation for prolonged periods without damage and allow pump restarts immediately.
The use of these pump wear parts results in lower operating and repair costs and provides protection against catastrophic failures.
This heater drain pump experiences constant use and is generally rebuilt every five to eight years. After this rebuild, the pump was put back into service and the power plant’s maintenance manager expects it will be another eight years before they have to rebuild it again. The bushings are intended to be the sacrificial wear part and have proven themselves as a great option for this type of application.
DS2175-58

|