GRAPHALLOY®
Solving Power Plant Damper Failures
Pre-heated secondary air makes the inlet-air section of a utility boiler hot...hotter, in fact, than most steel bearings can handle.
A power plant had difficulty operating the dampers that control the flow of preheated air into the combustors. The hot air quickly dried out the lubricant in the steel damper bearings, causing the dampers to seize.
The problem was solved by replacing the steel bearings with self-lubricating GRAPHALLOY® bearings. These new bearings have been in operation for years without a single failure.
Failing Dampers Hurt Productivity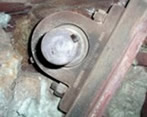
Secondary air accounts for 85% of the total combustion airflow to the cyclone burners. This air is heated to 650° F - 750° F (350° C - 400° C) by flue gas through a large heat exchanger. It then flows through a windbox duct to the cyclone burners where it is mixed with powdered coal. Airflow to each burner is determined by an 8’ by 6” by 2’ control damper. The dampers are not moved often and the grease quickly carbonized, locking the bearings.
The utility did not want to bring the unit offline for a bearing problem so it tried to make do. The plant was often forced to alter its firing methods.Frequently, the cyclone burners worked inefficiently due to the inability to control the combustion air. In some cases, it was necessary to fabricate a device to forcefully move a damper manually because operators could not budge them.
The Solution
The power plant solved the problem by replacing the lubricated steel bearings with self-lubricating GRAPHALLOY bearings. Of the 40 bearings used in the plant, 30 consist of three sizes of pillow block bearings while the other 10 are four-bolt flange block bearings.
The upgrade was accomplished during a planned outage. Initially, all of the bearings in one boiler unit were replaced. The GRAPHALLOY bearings ran without any problems and, one year later, the plant replaced the bearings in the other boiler.
The Benefits
The power plant experienced the following benefits by switching to GRAPHALLOY:
- The cyclone burners now operate more efficiently because the plant can precisely control the flow.
- Operators are now freed from the time-consuming and distracting task of manually operating the dampers and, when necessary, jerry-rigging devices to force the dampers to move.
- The plant has also had a substantial savings in costs for replacement bearings and labor.
Are you experiencing similar problems with heat and bearing failure? If so, the engineers at GRAPHALLOY will work with you to develop the right solution and help you beat the heat.
Click here to download this case history
|