GRAPHALLOY
®
Automotive Supplier’s Change to GRAPHALLOY
Bearings
Increases Production in High Temperature Furnace
Production has increased by several thousand units per month as a result of
eliminating failures in high temperature grease lubricated cam followers. A
change to GRAPHALLOY, a graphite/metal alloy bearing material, has helped TI
Automotive increase production in a heat shrink furnace that is critical to
their operation.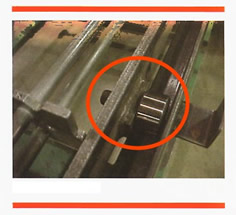
Before the change to GRAPHALLOY cam followers, the conveyor bearings failed
about once a month because the heat of the furnace evaporated their high
temperature grease lubricant. It took about half a day to cool down the furnace,
change the bearings and reheat the furnace so that production could be
restarted.
As one step in their production process TI Automotive applies heat shrinkable
sleeves to brake and fuel lines. The sleeves protect areas of the steel lines
that might be vulnerable to objects thrown up by the tires. The company’s plant
in Ashley, Indiana, applies heat-shrinkable tubing to the lines and then places
them on a conveyor that feeds them into a furnace heated to 350oF where the
plastic shrinks to conform to the steel brake and fuel lines
"The new bearings have already lasted for about five years without a single
failure," said Harry Foley, Process Improvement Engineer for TI Automotive based
in Ashley, Indiana. "They have eliminated the downtime that formerly plagued
this operation. Since we installed them I estimate we’ve saved well over 300
hours of production downtime that would have been lost if we had kept the old
bearings."
Automotive industry standard
The double-walled Bundyweld tube produced by TI Automotive has become the
automotive industry standard for brake and fuel lines and the company has also
pioneered quick connectors, anti-abrasion sleeves, corrosion coatings and
bundling. A continuous strip of copper plated steel is wrapped and bonded to
form a double-walled tube designed to carry fluids at high pressure, as well as
to provide greater assurance against leakage in low-pressure applications. The
latest manufacturing techniques have allowed for precise control of the
temperature and brazing conditions and can be coupled to other continuous
processes, such as coating.
Coatings enhance the proven integrity of Bundyweld tubing, giving protection
against corrosion and abrasion in extreme environmental conditions. All
underbody components, including the brake line, have the potential to be struck
by objects thrown up by the tires. TI Automotive provides extra protection
against damage by specifying the addition of a plastic sleeve to the tube areas
most vulnerable to stone damage. Sleeves can be applied to either add further
abrasion resistance in areas of high potential impact or to give
noise/vibration/harshness reduction benefits.
Protecting critical brake lines
When heated, the sleeve shrinks to conform to the size and shape of the
underlying material. The company uses a special furnace to increase the
productivity of the heating operation. The oven is open on both sides and has a
conveyor system that runs through the furnace and extends a distance on either
side. This highly efficient production heating process is capable of producing
between 3000 and 5000 parts per day depending on customer order levels.
Problems with downtime
In the past, the conveyor rode on ten standard cam roll bearings that were
lubricated with high temperature grease. The problem was that the heat caused
the grease to deteriorate and led to early bearing failure, typically after
about one month of use. The bearing replacement process typically took about
four hours, which resulted in a production loss of between 1500 and 2500 pieces.
In an effort to solve the problem, Foley tried many different lubricants but was
never able to find one that would last any longer than a month. He also tried
stainless steel bearings without any lubricant but found that they were also
unable to stand up to the application.
Then Foley searched an industrial directory for high temperature bearings and
found GRAPHALLOY, a high temperature graphite-metal alloy bearing material.
GRAPHALLOY combines the properties of graphite and metal. The graphite structure
can be compared to a deck of cards with individual layers that are able to
easily slide off the deck. This phenomenon gives the material a self-lubricating
ability that is matched by no other material. External lubricants are simply not
necessary. GRAPHALLOY is graphite filled with a metal impregnant to enhance the
chemical, mechanical and tribological properties of the material.
Solving the problem
Foley called up the bearing manufacturer and soon received an application
data sheet asking for information such as the inside and outside diameter of the
bearing, temperature of the application, operating speeds and loads, etc. He
filled out the form and faxed it back to Graphite Metallizing. The company
responded with a proposal that included drawings, operating specifications and
procedures. The bearing manufacturer said that they had no doubt that their
bearings would easily stand up to the application. Foley purchased 10 of the
bearings and installed them in the conveyors.
"The performance of the new bearings has been simply amazing," Foley said.
"We have gone from a situation where we had to change bearings every month to
one where the bearings never need changing. They have already been in operation
for more than five years and not a single one has failed nor have we seen any
signs of problems. The result is that we have been able to significantly reduce
production downtime. During the periods when our operators used to have to sit
on their hands waiting for bearings to be changed, they are now pumping out
parts."
Self-lubricating properties
GRAPHALLOY bearings are self-lubricating because when the bearing is rubbed
against metal or ceramics, a microscopically thin graphite film is quickly laid
down on the shaft. This low-friction film plays a vital role in controlling
temperature rise during operation. The formation of a proper transfer film
requires the presence of absorbable vapors such as water. Grades with special
impregnants are available for those rare applications in which no suitable
vapors are present.
This unique self-lubricating bushing material requires no grease or oil,
survives run-dry conditions, and eliminates galling and seizing in hot and dry
conditions. GRAPHALLOY is ideally suited to applications where temperatures are
too high to permit the use of oil or other lubricants because there are no
lubricants to congeal or solidify. GRAPHALLOY will not soften at high
temperatures or extrude under load. Many grades are suitable for temperatures to
750o F in air, where oil-based lubricants burn off or oxidize and plastics fail.
Special grades give good service up to 1000o F and higher in non-oxidizing
atmospheres.
The material provides other properties that are beneficial in this and other
applications. It maintains its integrity even when submerged in hostile liquids
such as acids, alkalies, hydrocarbons, black liquor, and liquid gases. The
material provides a constant, low coefficient of friction rather than just a
surface layer, helping to protect against catastrophic failure. Lubrication is
maintained even during linear motion; lubricant is not drawn out and dust is not
pulled in. GRAPHALLOY wear components also improve reliability under conditions
such as low speed operation, frequent starts and stops and switch-overs from
standby to continuous running. GRAPHALLOY bushings are available in over 100
grades of material in any desired size or geometry, including cylindrical with
or without grooves, flange or double flange, split and metal-backed. Grades and
design are engineered to best serve the application.
|